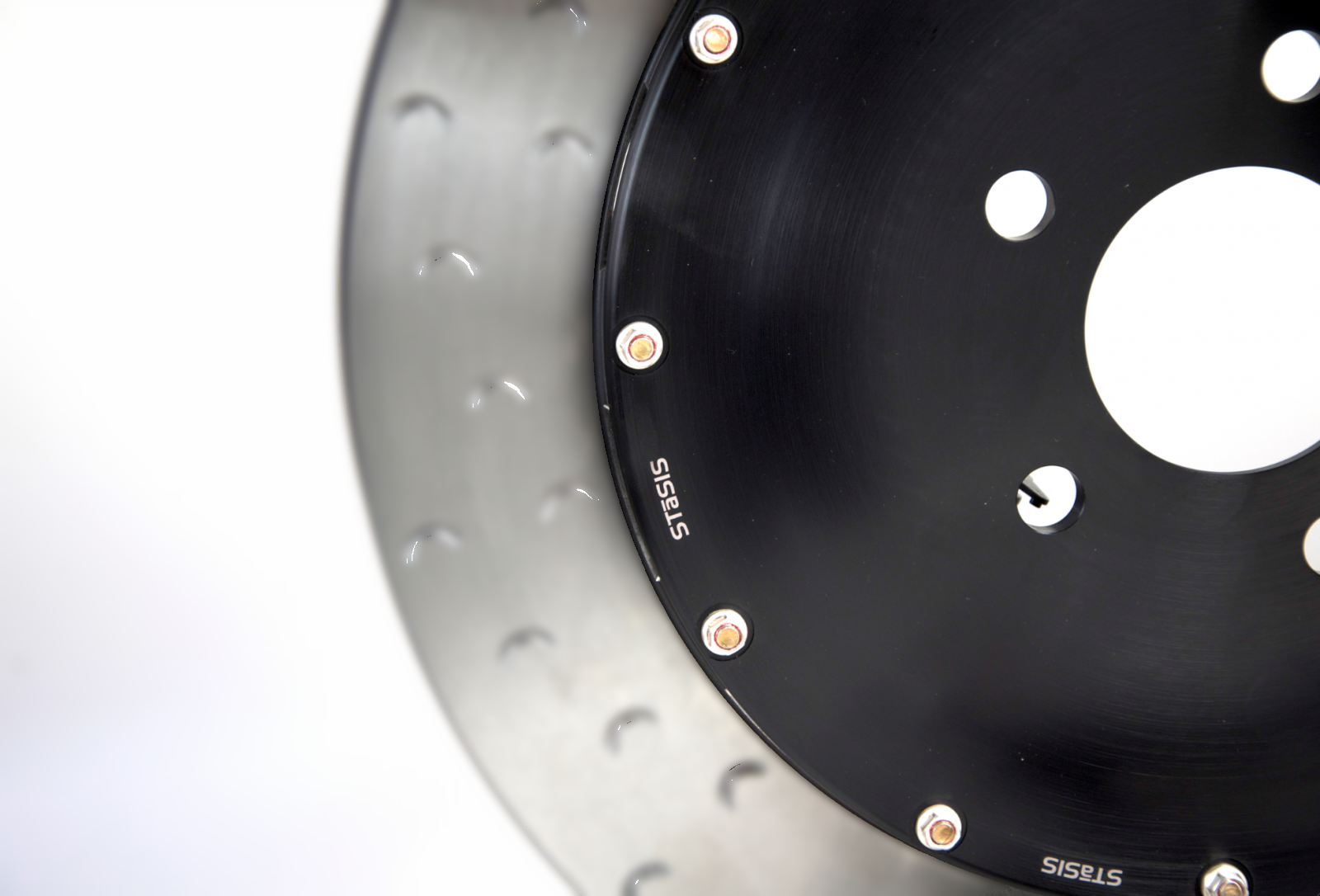
Glossary of Braking Terms
Glossary of Braking Terminology
By Stephen Ruiz and Carroll Smith
ABS: Acronym for Anti-Lock Braking system. Anti Lock braking systems sense the speed and rate of deceleration of each of the wheels of a vehicle independently and, through a microprocessor control system, act to prevent lock up of any of the tires under braking force by cycling the line pressure to the wheel that is approaching lock up. Most current passenger cars are fitted with ABS.
Aluminum Beryllium: A composite material of exceptional stiffness to weight ratio used for Formula One calipers (and Ilmor/Mercedes engine blocks) in the late 1990s. Now outlawed on health grounds
Aluminum Lithium: A composite material of exceptional stiffness to weight ratio currently being used for Formula One calipers.
Anti-squeal plates: Very thin stiff metallic or composite plates, sometimes coated with a high temperature solid lubricant, inserted between the pad backing plates and caliper pistons on passenger cars to reduce or eliminate brake squeal.
Asbestos: Impure magnesium silicate with very low thermal conductivity - once used as an insulating material and as one of the components in brake friction materials. Now outlawed on health grounds.
Backing plate: The steel portion of a disc brake pad which contacts the caliper piston(s) and to which the friction material is bonded. The backing plate provides the necessary stiffness and mechanical strength to the pad system. Its dimensions, flatness and surface finish must be closely controlled. The longer the pad, the thicker must be the backing plate. Backing plates of less than about 3 mm should be viewed with suspicion unless the pad is very short.
Bedding in: There are two types of "bedding in" with regard to brakes:
1. Bedding of the friction material. All friction materials contain volatile elements used as binders. In the initial thermal cycling of the material these volatiles boil off, forming a gaseous layer between the friction material and the brake. A bedded pad will exhibit a layer of discolored material from 1.5 to 3 mm thick.
2. Bedding of the disc. Before using a new disk, all machining and preservative oils must be completely removed following the disc manufacturer's recommendations. Usually it involves washing with soap and water or using one of the proprietary "brake clean" compounds. The disc should then be mounted and checked for run out. It should be bedded in with a number of moderate stops with lots of cool off time between stops, gradually increasing the severity of the stops until the entire surface of the disc is evenly discolored. This will prevent thermal shock, distortion and the formation of "hot spots" (regional deposition of pad material which results in a permanent transformation of the cast iron underneath the deposit) and ensure maximum disk life.
Bell: See "hat"
Bias bar: A system allowing rapid adjustment of the front to rear braking force on a car. Universal in racing, the bias bar connects the pushrods of dual master cylinders with an adjustable fulcrum allowing crew or driver adjustment of the braking ratio.
Bite: The speed at which the friction material reaches its maximum coefficient of friction when braking is initiated. The amount of bite is a compromise. Too much bite makes initial modulation difficult. Too little causes a delay in braking. In racing, different drivers prefer pads with different degrees of bite.
Blades: See "vanes"
Bleeding: The process of removing overheated fluid and air bubbles from the hydraulic system.
Bluing: Discoloring of cast iron rotors due to heat. Although bluing is evidence of thermal stress and will lead to reduced rotor life, it is normal under repeated hard braking and is not a cause for concern.
Brake bias: The term used to indicate the ratio between the amount of brake torque exerted on the front brakes compared with the rear. Brake bias is normally expressed as a percentage of brake torque at one end of the car to the total brake torque, as in "60% front".
Brake booster: A vacuum device that multiplies pedal effort at the cost of pedal travel and pedal firmness. Virtually universal on passenger cars.
Braking efficiency: The ratio of actual deceleration achieved on a given surface compared with the theoretical maximum.
Brake line pressure: The instantaneous hydraulic pressure within the brake lines. Brake line pressure in pounds per square inch is the force applied to the brake pedal in pounds time multiplied by the mechanical pedal ratio divided by the area of the master cylinder in square inches. For the same amount of pedal force, the smaller the master cylinder and/or the greater the mechanical pedal ratio, the greaterthe brake line pressure and the longer the pedal travel.
Braking torque: Braking torque in pounds feet on a single wheel is the effective rotor radius in inches times clamping force times the coefficient of friction of the pad against the rotor all divided by 12. Braking torque is the force that actually decelerates the wheel and tire. To increase the braking torque it is necessary to increase the line pressure, the piston area, the coefficient of friction or the effective rotor diameter. Increasing the pad area will not increase the braking torque.
Caliper: The "hydraulic clamp" portion of a disc brake system. Manufactured from either ferrous or nonferrous material and bolted firmly to the suspension upright (or "knuckle") the caliper holds the pads in place and, through the action of hydraulic pistons actuated by the master cylinder, forces them against the rotating surface of the disc when pressure is applied to the brake pedal.
1. Fixed caliper: A brake caliper in which two or more pistons are arranged on either side of a rigid body with the disc in the center. Due to its inherent stiffness the fixed caliper is the only design suitable for racing categories where it is allowed and is the preferred design for high performance cars.
2. Floating caliper: A design in which a single or dual piston is located inboard of the disc and the outer body of the caliper slides on suitable surfaces in reaction to piston pressure. The piston forces the inboard pad against the disc while the sliding outer body clamps the outboard pad against the disc. The inherent lack of rigidity in the design, compared to fixed caliper design, combined with the friction inherent in the sliding outer body makes this design less suitable for racing and high performance use. The design is well suited for use with front wheel drive as the absence of any outboard pistons allows greater negative (inward) wheel offset. In all applications, this caliper type is simpler to manufacture and affords more packaging flexibility for zero or even negative scrub radius front suspension designs. It is sometimes used in the rear on an application that has a fixed design in the front.
3. Open caliper: The design of fixed caliper in which the "window" through which the pads are inserted is structurally open. This design, while less expensive to manufacture, significantly reduces caliper rigidity.
4. Closed caliper: The design of fixed caliper in which the "window" through which the pads are inserted is structurally reinforced by a bridge.
5. Caliper bridge: The structural reinforcement across the open face of a fixed caliper. In order to be effective the bridge must be rigidly bolted in place with high tensile fasteners. Sliding - see Floating Caliper
Carbon/carbon brake: A braking system in which both discs and pads are manufactured from carbon composite material. Utilized in every form of racing where they are not outlawed, carbon/carbon brakes offer significant reduction in rotating mass and inertia along with much greater thermal capacity and dimensional stability in use. The disadvantages include cost, a certain amount of lag time while heat builds up (especially in the wet) and some difficulty in modulation. Contrary to popular belief, the coefficient of friction is no better than that of state of the art carbon metallic pads and cast iron discs. A major advantage on super speedways is the reduction of gyroscopic precession on corner entry.
Carbon metallic: This is a trademark of the Performance Friction Corporation. Pad friction compounds containing large percentages of pure carbon along with various metallic elements. Pioneered by Performance Friction Corporation these compounds offer very constant coefficients of friction vs. temperature characteristics along with increased thermal capacity. The disadvantage is that, since they both operate at higher temperatures and their temperature rises to operating temperature faster than other compounds, they increase thermal shock to the disc and increase thermal conduction to the caliper pistons and brake fluid. As a result, it is recommended to not use drilled discs with carbon metallic pads.
Cast iron: Metallic iron containing more than 2% dissolved carbon within its matrix (as opposed to steel which contains less than 2%)and less than 4.5%. Because of its cost, relative ease of manufacture and thermal stability cast iron (sometimes referred to as "gray cast iron" because of its characteristic color, but is actually a more specialized material for brake applications) is the material of choice for almost all automotive brake discs. To work correctly, the parts must be produced at the foundry with tightly monitored chemistry and cooling cycles to control the shape, distribution and form of the precipitation of the excess carbon. This is done to minimize distortion in machining, provide good wear characteristics, dampen vibration and resist cracking in subsequent use.
Ceramic buttons: Insulating buttons inserted in the face of racing caliper pistons to reduce conduction of heat to the brake fluid. Not currently in use, as Titanium buttons have proved more effective.
Ceramic coatings: Some racing calipers feature a ceramic coating sprayed onto the interior surfaces as a radiation barrier to reduce heat transfer from the disc and pads to the caliper and fluid.
Clamping force: The clamping force of a caliper in pounds is the brake line pressure multiplied by the total piston area of the caliper in a fixed caliper and two times the total piston area in a floating design. To increase the clamping force it is necessary to either increase the line pressure or the piston area. Increasing the pad area or the coefficient of friction will not increase clamping force.
Coefficient of friction: A dimensionless indication of the friction qualities of one material vs. another. A coefficient of 1.0 would be equal to 1g. The higher the coefficient, the greater the friction. Typical passenger car pad coefficients are in the neighborhood of 0.3 to 0.4. Racing pads are in the 0.5 to 0.6 range. With most pads the coefficient is temperature sensitive so claims that do not specify a temperature range should be viewed with some suspicion. The optimum is to select a pad with a virtually constant but decreasing coefficient over the expected operating range of temperatures. As a result, the driver does not have to wait for the pad to heat up before it bites, and the pad fade will not be a factor so that modulation will be easy (see "plot shape").
Compressibility: All materials are compressible. Under enough pressure the rock of Gibraltar will compress to some extent. It is important that the friction material of the pad not compress under the expected clamping force. If it does, pad wear will be uneven and braking efficiency will be compromised. Compressibility is seldom mentioned in advertising. It should be. Compressibility of a given material and the wear rates are the two primary factors that are considered in determining the size of a pad for a given application.
Conduction: One of only three heat transfer mechanisms. Convection and radiation are the other two. Conduction is the transfer of heat by physical contact. For example, some of the heat generated by the automobile braking system is transferred to the caliper pistons and thence to the brake fluid by conduction. Some of it is also transferred to the hub, upright (knuckle) bearings, and wheels in the same way. Two-piece or floating discs reduce conduction to the hub, and other parts because of the intervening hat. Conduction is also the strategy used in all designs to move the heat from the disc pad interface to the vanes and in some designs to provide the initial heat sink for the energy generated at the start of a braking cycle. The sacrifices made if this is the primary strategy used for heat transfer are the weight and inertial penalty in a rotating part.
Convection: One of only three heat transfer mechanisms. Conduction and radiation are the other two. Convection is the transfer of heat by fluid flow. Air can be considered to be a fluid in a thermal model of a brake system when it is moving and is contact with the heated surfaces of the disc or drum. In the case of a solid disc the air moving over the surface of the disc is very random and turbulent, but still functions to provide some cooling. In the case of a ventilated disc, by the pressure of a forced air duct or by induced flow that is a result of the centrifugal acceleration of the air already in the vent of a rotating disc, air flows through the vents. The air absorbs thermal energy along the vent path. In this way, the heat generated by the braking system of an automobile is transferred to the moving air stream and away from the brake disc.
Cracking: Cracking is primarily due to heat cycling that weakens the cast iron discs. The exact mechanism of this failure is disputed. Cast iron discs are formed with the excess carbon being precipitated in the form of carbon plates or flakes dispersed throughout the ferrite (iron) matrix. What is believed to happen is that when discs are operated above about 900º F, the carbon becomes more flexible or "fluid" in its shape partly due to the thermal expansion of the enclosing ferrite matrix. Then, as the disc cools relatively rapidly back below about 900º F the carbon is trapped in a changed more random shape then when it was first cast. This creates internal stress on the part and continuously transforms the disc by relieving the stress through the cracking. The cracks begin by appearing between carbon flakes. Nodular or ductile iron would resist this cracking due to the excess carbon being precipitated in a spheroid form, but it, like other alternative materials do not have the mechanical properties needed to function ideally in a brake disc application. In discs that are cast to resist cracking through chemistry and controlled cooling at the foundry, cracking will still occur, but more slowly and take the form of heat checks on the surface. In some cases cracks will begin at the periphery of the disc and propagate inwards. In this situation, propagation can be delayed by drilling small holes at the end of the cracks (stop drilling). We do not recommend this however, because if the cracks continue to propagate unnoticed, catastrophic mechanical failure will result. Replace disc at the first sign of cracks at the outer edge of any size. A historic note, the original purpose of the curved or angled vane disc was to prevent cracks from propagating by imposing a solid vane in the path of the crack. The cooling function was secondary.
Cryogenic treatment: A thermal process in which metallic components are slowly cooled to near Kelvin temperature and then equally slowly returned to room temperature. Proponents claim that the grain structure is refined by the process. There is considerable doubt about the effectiveness of the process. Evidence is largely anecdotal and to date no scientific and quantitative engineering studies have been published.
Differential bores: The leading edge of a brake pad wears faster then the trailing edge. This is due to the migration of particles of incandescent friction material carried from the leading to trailing edge of the pad. In effect the trailing portion of the pad is riding on a layer of incandescent material. By providing an optimally designed larger caliper piston at the trailing edge of the pad, wear can be evened along the length of the pad
Disc: The rotating portion of a disk brake system. Mechanically attached to the axle, and therefore rotating with the wheel and tire the disc provides the moving friction surface of the system while the pads provide the stationary friction surfaces. Except for racing, discs are normally manufactured from one of several grades of cast iron. Some European front drive passenger cars, where the rear brakes do very little work, are using aluminum metal matrix rear discs to save weight. Most professional racing cars use carbon/carbon discs.
1. One-piece disc: A disc cast in one piece with its hat or bell. This is the inexpensive way to manufacture a disc and is perfectly adequate for normal use. There are some tricks to the design to reduce distortion.
2. Floating disc: The norm in racing, the floating or two-piece disc consists of a friction disc mechanically attached to the hat either through dogs or through drive pins. Properly designed this system allows the disc to dilate (grow radially) without distortion and to float axially, greatly reducing drag.
3. Solid disc: A disk cast as a solid piece suitable for light cars not subjected to extreme braking.
4. Ventilated disk: A disc cast with internal cooling passages. The norm in racing, high performance and heavy vehicles.
Drilled or cross-drilled rotors: Disks that have been drilled through with a non-intersecting pattern of radial holes. The objects are to provide a number of paths to get rid of the boundary layer of out gassed volatiles and incandescent particles of friction material and to increase "bite" through the provision of many leading edges. The advent of carbon metallic friction materials with their increased temperatures and thermal shock characteristics ended the day of the drilled disc in professional racing. They are still seen (mainly as cosmetic items) on motorbikes and some road going sports cars. Typically in original equipment road car applications these holes are cast then finished machined to provide the best possible conditions by which to resist cracking in use. But they will crack eventually under the circumstances described in another section (see Cracking). Properly designed, drilled discs tend to operate cooler than non-drilled ventilated discs of the same design due the higher flow rates through the vents from the supplemental inlets and increased surface area in the hole. That's right, inlets, the flow is into the hole and out through the vent to the OD of the disc. If discs are to be drilled, the external edges of the holes must be chamfered (or, better yet, radiused) and should also be peened.
Drum in hat: A disc design in which the internal surface of the hat serves as a brake drum. Often used as a parking brake.
Dust boots: Rubber shields that fit over the exposed portion of the caliper pistons to prevent the ingress of dust and road crime. As no known rubber compound will withstand the temperatures generated by racing brakes, dust boots are not used in racing and should be removed before truly hard driving for extended periods.
Effective temperature range: The range of operating temperatures within which a pad material remains effective. As with coefficient of friction, this should be used for comparative purposes only as measurement procedures very between manufacturers and pad temperatures are strongly affected by disc mass and rate of cooling.
Ether based brake fluid: "Normal" brake fluids are based on Alkyl Polyglycol Ether Esters. Also, sometimes referred to as Glycol Ether Borate Ester fluids. DOT 3 and DOT4 fluids are suitable for high performance passenger car use.
Friction consistency: The variation in coefficient of friction over a range of repeated stops. Minimum variance allows efficient brake modulation.
Friction Mechanisms: For a pad and disc to function as a brake there has to be the conversion of kinetic energy to heat. There are two primary models of the mechanism of this conversion; both involve the breaking of bonds to release energy. In the case of the abrasion model the bonds broken are the ones already existing in a materials. The bonds are broken due to the chafing or abrasion of a harder material or particle in direct contact with it. The second model is the adhesion-breakage model where temperature and pressure at the interface between the pad and disc surface cause the fusion of one material to the other or the diffusion of one material into the other. In this case, the instantaneous bonds formed in the process are broken releasing energy. Pad materials function using both models at the same time or at different times. The abrasive mechanism predominates at lower temperatures but is also necessary to control build-up of low melting point pad materials at elevated temperatures where the adhesionbreakage mechanism is thought to predominate. The adhesion-breakage model requires a transfer layer of pad material to be established on the disc surface to function unless the brake system is designed so that the disc is fusing into the pad. The latter is the case with many high dusting European automotive designs where the disc wears observably as the pad wears. The iron in these discs is typically a "softer" more dampened form of cast iron.
Fade: Loss of braking efficiency from excessive thermal stress. There are three separate and distinct types of brake fade: 1. Pad fade: When the temperature at the interface between the pad and the rotor exceeds the thermal capacity of the pad, the pad loses friction capability due largely to out gassing of he inding agents in the pad compound. The brake pedal remains firm and solid but the car won't stop. The first indication is a distinctive and unpleasant smell, which should serve as a warning to back off.
2. Fluid boiling: When the fluid boils in the calipers, gas bubbles are formed. Since gasses are compressible, the brake pedal becomes soft and "mushy" and pedal travel increases. You can probably still stop the car by pumping the pedal but efficient modulation is gone.This is a gradual process with lots of warning.
3. Green fade: When the pad is first placed in service the first few heat cycles will cause the volatile elements of the material to out gas. The process is continuous throughout the service life of the pad, but it is most pronounced in the bedding in process when the outgassed materials form a slippery layer between the pad and the disk reducing the coefficient of friction to near zero. Once the pads are bedded in out gassing is so slow as to not be a problem unless the effective temperature range of the pad is exceeded.
Fireband: The name given to the boundary layer of out gassed volatiles and incandescent particles of friction material that rotates with the disc.
Glycol brake fluid: See "ether based brake fluid"
Grooves: See "slotted"
Grooving: A wear pattern of concentric grooves on the surface of a disc. This can be caused by inclusions within the pad material, inappropriate pad material for the operating conditions. Poor initial machining of the disc and/or improper bedding in procedure. Not a major cause for concern on passengercars.
Heat checking: The precursor to cracking. Heat checks are actually surface cracks caused by thermal stress. By themselves heat checks are not a cause for concern but they are a warning sign that the disk is not receiving adequate cooling air and cracks are sure to follow. See also the section "Cracking".
Hydraulic ratio: The ratio of fluid displacement by the master cylinder to fluid displaced in the caliper pistons. Hydraulic ratio is an important factor in the pedal effort equation, the higher the ratio, the less pedal effort is required (and the longer the pedal travel to achieve a given clamping force). The stiffer the caliper and the stiffer the pad, the higher the hydraulic ratio that can be employed.
Hygroscopic: The property of readily absorbing water. All non silicon based brake fluids are hygroscopic in nature. The adsorption of a minute amount of water will dramatically lower the boiling point of brake fluid. For this reason brake fluid should be completely replaced annually or more frequently in conditions of severe use. In professional racing, the fluid is replaced at least daily.
Knock back springs: Small coil springs fitted inside the caliper pistons of some brakes to prevent the pads from excessive knock back from flexing of the suspension system or run out in the discs. If the disc run out is within specification and the upright/axle assembly is sufficiently rigid, there should be no need for knock back springs. However, when operating conditions are severe with regard to either generated side force or bumps, they may be required on the best of designs.
Leading edge (of pad): With respect to disc rotation the leading edge is that edge of the pad that first comes into contact with the disc when pedal pressure is applied. Unless multiple pads or differential piston diameters are used the leading edge wears faster than the trailing edge. See "Differential pistons" and "Taper wear".
Line pressure: See "Brake line pressure"
Master cylinder: The hydraulic cylinder that transmits and multiplies the driver's pedal effort to the operating end of the braking system at the calipers.
Material transfer: Please see "Friction Mechanisms", where beneficial material transfer is discussed in context with the adhesion-breakage model. Otherwise, when the operating temperature of the pad (particularly organic pads) is exceeded, friction material may be deposited onto the surface of the disc in a non-uniform manner while degrading the braking capacity and causing noticeable roughness. The only cure is to either upgrade the pad material or increase the cooling (or both). "Pick up" should never be removed with ordinary sandpaper, which uses aluminum oxide as the abrasive. The same is true of sand blasting, don't do it. The correct way to remove pick up is by grinding (not turning) the disc. When that is not practical, the major portion can be removed by scraping and the remained sanded off with garnet paper.
Mechanical pedal ratio: The brake pedal is designed to multiply the driver's effort. The mechanical pedal ratio is the distance from the pedal pivot point to the effective center of the footpad divided by thedistance from the pivot point to the master cylinder push rod. Typical ratios range from 4:1 to 9:1.The larger the ratio, the greater the force multiplication (and the longer the pedal travel)
Metal matrix (MMC): Term applied to a family of composite materials consisting of metallic cores infused with "whiskers" or "grains" of very stiff non-metallic elements resulting in a light and strong material. The most popular of the metal matrix composites is Aluminum Ceramic metal matrix, the ceramic typically but not exclusively being composed of Silicon Carbide, Aluminum Oxides and Boron Carbides, which are well suited for use in racing calipers. Also, lightweight disc have been made for Original Equipment and aftermarket applications using Silicon Carbide and Aluminum Oxides, but with only limited success due to two factors. The first being a low maximum operating temperature of the materials mentioned of around 900 o to 1000o F. Second the much greater expansion rate of the typically aluminum based MMC material results in thermal distortion or cracking. One OE application actually has small slots and stop drill holes positioned radially around the disc periphery. In all cases of MMC discs, the primary friction mechanism is the adhesion-breakage model. Please refer to the section, "Friction Mechanisms".
Modulation: The term given by the process by which the skilled driver controls the braking torque to maintain maximum retardation without locking wheels. Because the human being modulates most efficiently by force rather than displacement, effective brake modulation requires minimum pedal travel and maximum pedal firmness.
Monobloc caliper: A caliper machined from a single piece of billet, cast or forged material.
Multi pad systems: Caliper systems utilizing multiple pistons (either four six or eight) with separate pads and abutment systems for each pad. The design, almost universal in professional racing, provides multiple leading edges for better "bite". At the same time the very short pads ensure even longitudinal wear without the necessity for differential piston diameters
OE: This is an abbreviation for Original Equipment. Please see the section "Original Equipment". Sometimes it is used as an abbreviation to refer to the Original Equipment Manufacturer (but more correctly referred to as the OEM).
OEM: This is an abbreviation for Original Equipment Manufacturer.
Off brake drag: A condition in which the caliper pistons do not fully retract when line pressure is released. Off brake drag increases temperature and wear while decreasing acceleration, top speed and fuel mileage. It is caused by either non-optimum seal design, seals that have been hardened by thermal stress or excessive disc run out.
Original Equipment: This is an industry standard term for that equipment that was installed on the model(s), being referred to in context, at the time of manufacture.
Organic (pad material): A family of friction materials, often containing asbestos, used for both drum linings and disk pads through the 1980s. Now largely replaced by semi-metallic materials with better temperature characteristics.
Outgassing: The boiling off of the volatile elements in friction materials. Out gassing, while it is continuous over the useful life of the pad, is only noticeable during the bedding in process or when the temperature capability of the pad has been exceeded. Under those conditions the volatiles form a layer between the friction materials and the disc surface, smelling bad and causing "green fade".
Pad: The stationary element of the disk brake system. The pads, consisting of friction material bonded to steel backing plates are held in place by the caliper and forced against the disc by the caliper pistons when pedal pressure is applied.
Pad abutments (or pad abutment plates): Mechanical elements that locate the pads in the caliper and provide hard surface for the pads to slide against. Non-ferrous (Aluminum or MMC) calipers, which do not provide hard and smooth surface to locate the ends of the pads and provide an efficient sliding surface, should be viewed with great suspicion.
Pad retraction: To prevent drag and premature pad wear the properly designed seal systems retract the caliper pistons a few thousandths of an inch when the pedal pressure is released. This allows what little disc run out there is to "knock" the pads back from contact with the disk. When everything works right the amount of retraction is so slight that the free play in not noticeable when pedal pressure is applied.
Pick up: See the section Material Transfer.
Caliper Pistons: The hydraulic cups that transmit line pressure to the pads to clamp the pads against the rotating disc. Manufactured from Aluminum, steel or Titanium and sealed in the caliper bores, the mechanical design of the piston is critical. The inescapable drag of the pad against the disk tends to "cock" the piston in its bore so the piston to bore clearance, thermal coefficients of expansion between piston and caliper as well as seal design and location are crucial.
Plot shape: The shape of the friction plot during a long brake application it is easier and more efficient for the driver to add pedal pressure than to remove it. Therefore the easiest pad to modulate exhibits a high initial bite followed by a gradual decrease in coefficient throughout the stop. If the level of friction rises throughout the stop, brake modulation will be very difficult.
Pressure bleeder: A tool allowing rapid bleeding of the system and replenishment of the fluid. Pressure bleeders should never be used on racing or high performance cars as the rapid forcing of the fluid through small passages may cause cavitations and the formation of air bubbles rather than their removal.
Proportioning valve: A rear brake line proportioning valve is found on most cars that do not feature anti lock brakes. Its function is to limit the amount of pressure transmitted to the rear brakes under very heavy retardation. Front and rear line pressures are the same until some pre-determined "knee" point is reached. After this point, rear line pressure, while it still increases linearly with pedal effort, increases at a lower rate than front. The purpose is to avoid rear wheel lockup and the attendant unstable oversteer. It is not a good idea to remove the proportioning valve from a road going automobile for highway use. If you feel that you must do so, the best way is to remove the OEM rear brake line proportioning valve completely and replace it with one of the adjustable units manufactured by Tilton Engineering or Automotive Products. Do not place a second proportioning valve in line with the OEM unit.
Radiation: One of only three heat transfer mechanisms. Conduction and Convection are the other two. Radiation is the transmission of energy by the emission of waves. In the case of braking systems, thermal energy is emitted by both the discs and the pads at elevated temperature. In the case of the disc, as temperature increases, radiation is the predominant heat transfer mechanism. The focus in disc designs is on the vent or the vanes because it is something that can be changed significantly at a reasonable cost. While radiation is a function of the material choices made, keeping in mind the other functional parameters necessary for the application. A large portion of this radiant energy can be reflected into the air stream by "radiant barriers", such as ceramic coatings on the internal surfaces of calipers.
Release characteristics: The opposite of "bite", release characteristics become important when braking into turns either on the track or on the road. If the braking torque does not decrease linearly with decreasing pedal pressure "trail braking" becomes difficult at best.
Reservoir: The container in which brake fluid is stored to provide a source of fluid for the master cylinder(s). The reservoir must have sufficient volume to allow fluid displacement equivalent to wearing the pads down past the backing plates. It must also be sealed to prevent the absorption of moisture by the highly hygroscopic brake fluid. Typically the reservoir cap is fitted with an electrometric bellows open to atmosphere but sealed from the fluid.
Residual pressure valve: Some passenger cars, particularly those equipped with drum rear brakes, are fitted with a "residual pressure valve": which functions to ensure that the pads are kept in close proximity to the discs despite run out, knock back, etc. The residual pressure is very small (2-4psi.) so off brake drag is not a problem for street use.
Rotor: see "Disc"
Run out: The amount of axial dimensional variation of the surface of the disc as it rotates. Measured with a dial indicator, normal specification is 0.000 to 0.005" total run out. Excessive run out results in inefficient braking and perceptible pedal pulsation.
Seals: Caliper pistons are sealed in their bores by electrometric rings seated in grooves. The seals fulfill a secondary function of slightly retracting the pistons when line pressure reduced to zero at the end of braking. This prevents "off brake pad drag", reducing both temperature and wear. Both the compound and the mechanical design of these seals are critical. The cross section of properly designed caliper seals is square, not round. "O" rings cannot be substituted.
Seal grooves: The caliper seal grooves can be either in the caliper bore or on the piston (or both). The mechanical design of the grooves is critical to ensure optimum piston retraction. The cross section of a proper caliper piston seal groove is trapezoidal, not square.
Semi-metallic: Friction materials compounded with significant amounts of metallic elements to increase the operating temperature range.
Silicon brake fluid: Brake fluid based on silicon. While silicon based fluids are less hygroscopic than ether based fluids, they are subject to "frothing" when subjected to high frequency vibration and when forced through small orifices. This makes them unsuitable for racing or high performance use. Sliding caliper: See "Caliper, Floating Caliper"
Slotted:
1. Disc: Shallow, sharp edged but radiused bottom grooves milled into cast iron discs to provide leading edges for bite and a path for the fire band of gases and incandescent friction material to be dissipated through. If the slots fill up with pad material, the system is operating at too high a temperature.
2. Pad: Radial grooves molded or cut into the surface of the pad to provide a path for fire band dissipation and to double the number of leading edges and improve bite. Some long pads also have a longitudinal groove.
Squeal: Annoying high-pitched noise associated with some combinations of friction materials at low brake torque values. Reduced by the use of anti squeal plates. Can be improved by a different pad material, but also made worse if the former and current pad materials are incompatible.
Squeeze form casting: A casting process that is a cross between die casting and forging. Liquid aluminum is poured into a die and, just before it begins to solidify, the die is forced closed under very high pressure. Alternatively a second cylinder is filled during the molding other than the primary injection cylinder that is then compressed at high pressure to increase the molding pressure. The process reduces porosity and leaves the grain structure more like a forging than a casting - resulting in a stronger and stiffer part.
Stainless steel brake lines: Flexible brake hoses made of extruded Teflon™ protected by a tightly braided cover of stainless steel wire. Because these hoses virtually eliminate line swelling under pressure, they are universally used in racing applications to reduce pedal travel, increase pedal firmness and allow more efficient brake modulation. A few manufacturers offer stainless steel braid protected hoses of extruded Teflon, which meet all of the DOT requirements for passenger, car use. Several more offer hoses that claim to meet the specification but do not. Let the buyer beware.
Stiffness: Stiffness is the resistance of a material or a structure to deformation. It is not the same as strength. The stiffness of a material is indicated by its "modulus of elasticity" - the measure of the elasticity of the atomic bonds within the material. It is essential that calipers (and caliper mountings) be stiff. Which is why metal matrix composite materials are used for racing calipers.
Strength: Strength is the resistance of a material or structure to rupture. It is defined as the stress required to rupture the atomic bonds of a material. It is not the same as stiffness.
Taper wear: Uneven wear of brake pads caused by geometry, by the difference in temperature between leading and trailing edges and/or by lack of stiffness in the caliper. When pads are taper worn, the first increments of caliper piston travel are used up in forcing the pad against the disc, increasing pedal Travel.Additionally the piston tends to cock in its bore resulting in bore scoring and wear.
1. Radial taper: Radial taper is apparent when the pad is viewed from either end. The linear speed between pad and disc is greater at the periphery of the disc and so the outer surface of the pad wears faster. In addition any tendency for the caliper to "open up" under pressure like a clamshell results in more pressure being placed on the outer portion of the pad, further increasing relative wear. For this reason many pads are trapezoidal in plan view with less surface area toward the inside.
2. Longitudinal taper: Longitudinal taper is apparent when viewed from either the inner or outer surface of the pad. The trailing section of the pad is partially floated in the boundary layer of out gassed volatiles and incandescent particles of friction material torn from the leading section. The leading edge of the pad will therefore always run hotter and wear faster than the trailing edge. This phenomenon is more pronounced in long pads and is one of the major reasons why racing calipers are designed with a multitude of small pads. (See "Multi piston calipers")
Thermal shock: Disc materials, particularly cast iron are degraded not only by the magnitude of temperatures reached, but also by the "delta" temperatures the speed at which the temperature increases and decreases. Cracks are largely caused by weakening of the bonds between the grains of the metal brought about by rapid change in temperature.
Threshold braking: Braking at maximum possible retardation in a straight line.
Titanium: A very light, very strong metal will very low thermal conductivity. Almost universally used to make caliper pistons for racing applications in order to reduce heat transfer to the fluid within the caliper.
Trail braking: The process in which the skilled driver "trails off" the brakes as he enters a corner, thus combining braking and turning in the initial phase of the corner and maximizing the total traction available from the tires. The technique, universal in racing, although not always admitted, also effectively lengthens the straight preceding the corner.
Trailing edge (of pad): That portion of the pad located away from the direction of rotation of the disc.
Two part caliper: A caliper manufactured from two essentially mirror imaged parts rigidly bolted together. To perform as well as a monolithic caliper, the assembly must result in a rigid structure by design, bolt selection and materials.
Vanes: The term given to the central webs which serve to separate the inboard and outboard friction surfaces of ventilated disks
1. Straight vanes: Straight vanes are the easiest to manufacture. They extend in straight lines radially outward from the inner surface to the outer surface of the disc. This design is often used in production automobiles and trucks because the same part can be used on both sides of the vehicle.
2. Curved vanes: Curved vanes are shaped as curves to act as more efficient pump impellors and increase mass airflow through the central portion of the disc. They also act as barriers to the propagation of cracks caused by thermal stress and, as each vane overlaps the next, they dimensionally stabilize the disc. Curved vane discs are more expensive to produce that straight vanes and must be mounted directionally. They are universally used in racing where carbon/carbon brakes are prohibited.
3. Islands: Some designs utilize "islands" to separate the friction surfaces rather than vanes. Properly designed the island system is dimensionally stable but inefficient from the viewpoint of airflow.
4. Differential vanes: Some discs are designed with alternating vanes of different length. This modern design feature that was the dictated by flow studies. It was found that the volume of air that a disc can flow increases by alternating the length of the inlet without much of a sacrifice in surface area. The more air a vent flows, the more convective cooling can be realized.
Wear sensors: To ensure that pads are replaced before they are worn down to the backing plates, several types of wear sensors are employed. Most production cars are designed with a float in the master cylinder reservoir. When the pads have worn to the minimum permitted thickness, enough fluid has been displaced to ground the float and complete an electrical circuit that activates a warning light on the dash. Alternatively some cars use an electronic wear sensor in the pad. This type of sensor typically is worn through when wear limits are reached, breaking continuity in the sensor circuit. As such, it needs to be replaced if the light has come on. There is another less expensive method used where the pad has a thin but stiff tab riveted to the pad backing plate that rubs on the disc face and squeals when the wear limit is reached. In some modern racecars used in long distance events, calipers are fitted with more complex electronic sensors and circuitry to warn the drivers and, by telemetry, the crew of the pad condition.