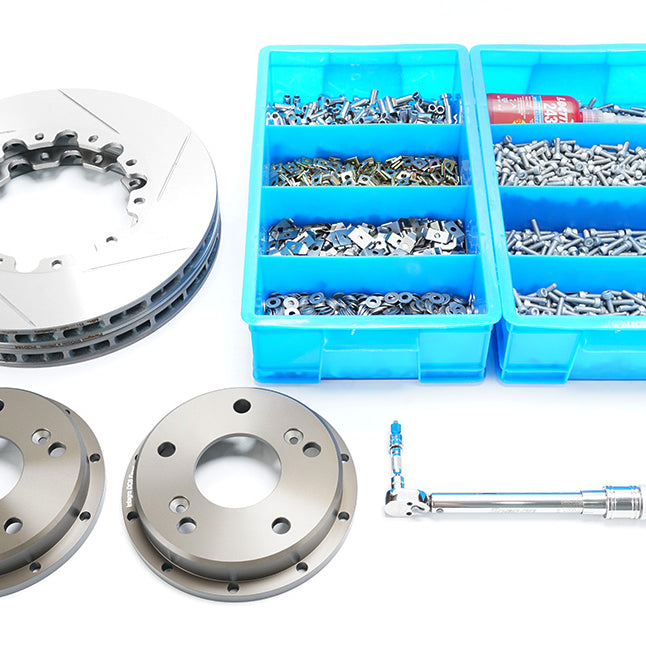
Bobbin Installation Instructions
Read these instructions completely before assembly. Installation and assembly of any brake component should only be performed by qualified professionals or with experience in the installation and assembly process of automotive components. These components will not function as intended if...