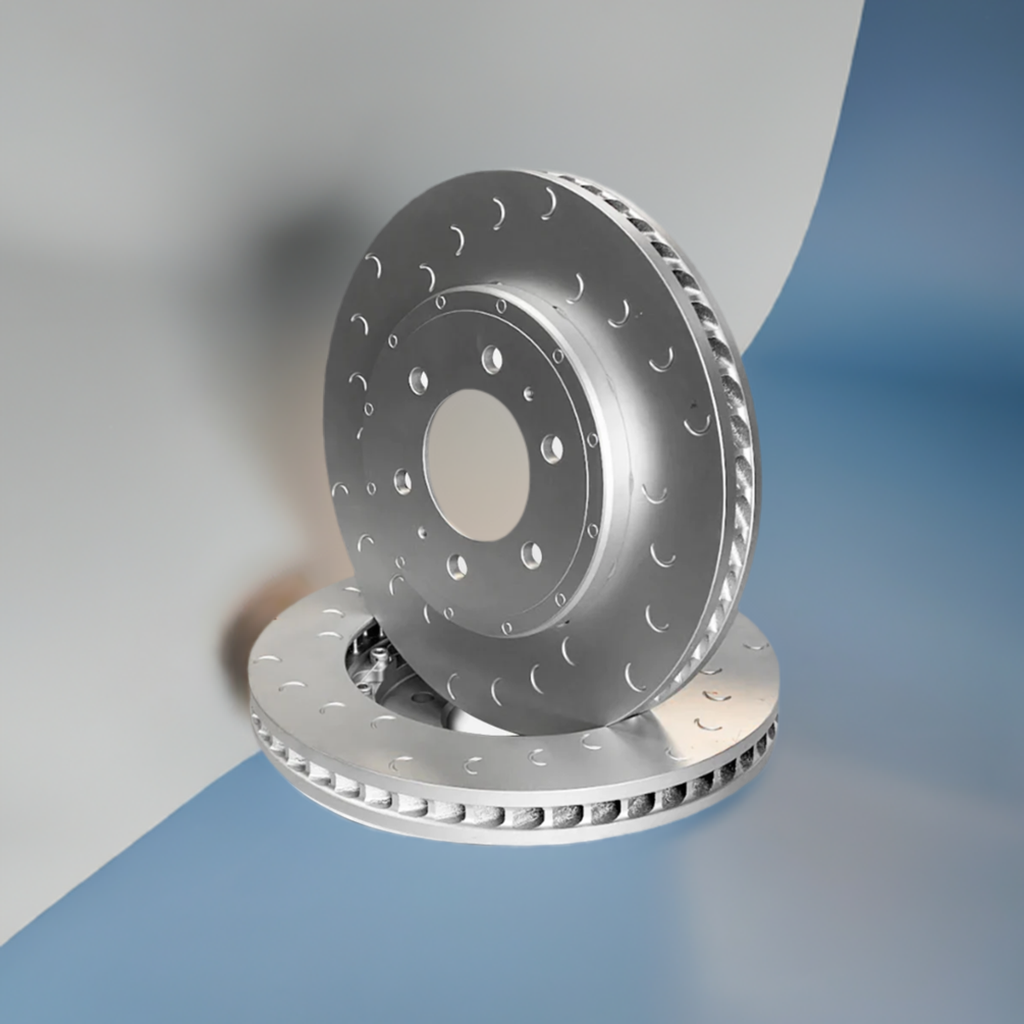
Pad and disc lifespan considerations by Alcon Chief Engineer, Michael Jones
Michael Jones, Chief Engineer (Special Vehicles) at Alcon UK talks about disc and pad life. Often the lifetime of discs and pads can vary widely, read on to find out why.
Part 1 - When the system is specified correctly, and the most appropriate pad material is chosen.
During the design phase, customers will often ask what the life of brake pads and discs will be. The answer is not as straight forward as many would think.
It is not unusual to see extreme differences in pad life for the same brake on the same vehicle. As an example, customers A, B & C may have to change their SUV’s pads after 800km, 30,000km and 80,000km respectively.
- Customer A may be driving their vehicle in a quarry.
- Customer B may be driving on a variety of tarmac, urban and rural roads.
- Customer C may be driving mainly on motorways.
Environment:
Some driving environments generate an aggressive paste between disc and pad that continually grinds the pad and disc, even when the brakes are not being applied. We call this 'off-brake wear'. Typical extreme environments where this may occur include quarries. Driving in any off-road or dirty road conditions will accelerate wear. The nearside brake pads generally wear quicker than off-side as dirt collects more at the side of the road than the centre.
Driving style:
Brake pad and disc life is not directly related to distance travelled. The number of brake applications and their severity can vary significantly. If a driver is continually making heavy braking events or holding the pedal on, then they are not only wearing the pads by the number of applications but accelerating the wear by running the brakes at a higher temperature. Brake pads wear quicker at higher temperatures. We have seen, in controlled tests where drivers run the same vehicle, on the same route, to the same speeds differences of around 25% in pad wear where the only difference is the driving style of different people.
Brake drag:
If for any reason, the pad is continually in contact with the disc, the pad and disc will wear more quickly due to friction and temperature. This could be from some sort of locked pressure, seized piston, seized pad, etc.
Drum brakes have similar issues with the drums and shoes. The drum can protect the shoes in some environments, but allow more dirt to collect in others.
Brake manufacturers have standard tests that allow us to compare, in a controlled environment, pad and disc wear.

Part 2 - When the system is not correctly specified and/or the choice of friction material is wrong.
Wrong size pads and discs:
Pad area is key. Too small a pad area and the friction material will work too hard and wear more quickly. Brake engineers have targets for pad work rate. This is measured in W/cm^2 or HP/in^2. Discs running at higher temperatures can also cause high wear.
Wrong pad and disc materials:
Although traditional brake discs are made from grey cast iron, the specification itself is wide. Brake manufactures will have standards that have tighter limits within this specification. The different specifications will have different wear rates and these will vary depending upon pad friction choice.
Different pad materials wear at different rates, so choosing the best for a specific application is important. A material that works well and has low wear on one application may be poor on another.
Some high performance pad materials may see ‘cold wear’ if the pad area is too small. The composition of the materials will work better at higher work rates and disc temperatures, but may grind the discs and pads when run cold.

Insufficient roll back of the seal:
The seal and seal groove technology is key to how the caliper behaves. The grove is designed so that the seal pulls back the piston into the caliper when pressure is released. If roll back is too big, then the travel at the pedal can be too long before the brakes start to apply. If it is too small then the brakes can drag when pressure is not applied. This is called ‘off-brake drag’.
Again, drum brakes have similar issues with the drums and shoes. Work rates, temperatures, materials and the mechanisms that pull shoes back from the drum are key to reducing wear.
The total design should take into account these issues, but there may be a compromise to get acceptable performance, feel and noise. Brake manufacturers have standard dynamometer tests that allow us to compare, in a controlled environment, pad and disc wear.
Part 3 - New technology
There is a drive to reduce brake emissions that has been highlighted by their use on full electric vehicles, where the biggest emissions now come from tyres and brakes.
Disc materials and coatings:
For many decades, grey cast iron was the best material for brake discs. When present, coatings were only for corrosion and were mainly sacrificial. New materials and coatings that give a much reduced wear are available, with some already in use. Many are also lighter in weight and help with point 6 below.
Pad friction materials:
Friction material manufacturers are constantly developing new materials that are better for the environment with regards wear and material content.

Regenerative braking:
Over 90% of brake events are at below 0.3g. Many EV manufacturers claim regen levels of up to 0.3g. The more braking that regen does or helps with, the bigger the reduction in disc and pad wear.
Autonomy:
Vehicles are gradually being equipped with new autonomous technology. Initial levels, that will keep vehicles to speed limits, will reduce wear by reducing the work done by the brakes reducing high speed brake events. More advanced levels will remove the human driver and introduce more efficient driving and braking.
Brake-by-wire:
By disconnecting the pedal from the wheel brakes, brake feel will be simulated. This means that clearances between pad and disc can be better defined with regards drag and off-brake wear.
Weight-saving:
Any saving in vehicle weight will mean that the brakes will use less energy to stop the vehicle.
All of the above need to be considered as part of the whole system. Weights, friction coefficients, etc. will change meaning that sizing in the specifications will need to be considered. This is only an brief overview of what vehicle and brake manufacturers are looking at in order to reduce wear.
